The first task was relatively easy: Open up the camera by removing the 6 tiny screws (use a size-0 Philips screwdriver for this, other cameras might even require size 00 and be prepared that you might need to apply some force. Be sure to use a screwdriver of the correct size to avoid that the heads get damaged) and remove the front and back housing. The plate connecting the switches can then be easily removed and the switch board can be seen. After using a multimeter to measure the contacts on this board, I obtained the following diagram:
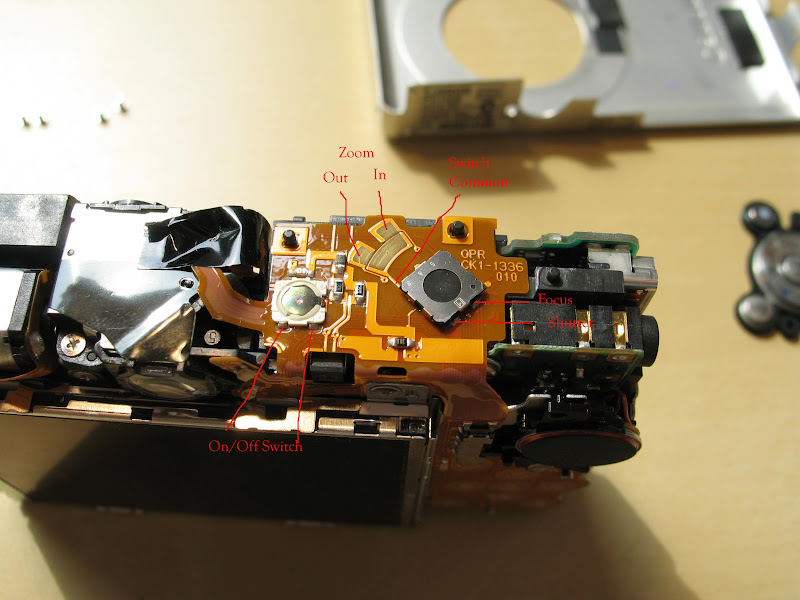
The next step was by far the most difficult: How to connect the switches of two tiny little cameras without damaging too much and without using a direct cable connection that would prevent the cameras from being usable alone? After researching many different connector designs I ended up with multipin- and multipoint connectors having a 1,27mm grid:
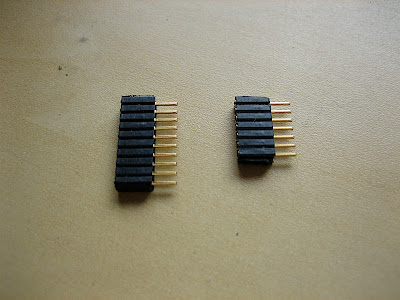
The only place to put the connector is directly above the usb and video socket where normally the rubber socket-cover is connected to the housing. This is the only part we need to get rid of. First we have to remove the small plastic pin that holds the rubber cover in place using a sharp knife:
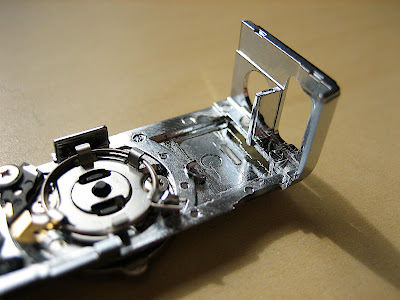
Afterwards you can see that the connector (after being shortened to 7 pins) would fit nicely into the resulting space:
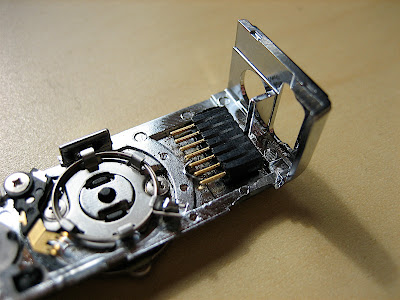
Most important thing however is that this connector can be reached from the outside simply by plugging a 7-pin multipin connector into the slot where the rubber cover used to be.
We now must make a little more additonal space inside above the USB and video ports: Remove the top 1mm of the plastic part between both ports:
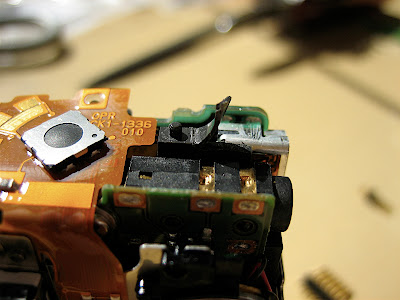
After shortening two of the seven pins of the connector and making it just a little slender using a rasp, it fits nicely into the resulting space and should be glued there using a tiny portion of superglue:
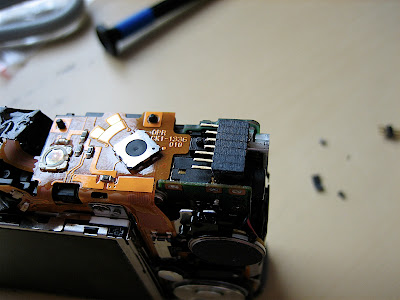
Now the even more delicate work begins: For the internal wiring I used leads from a 100pin ide cable which is relatively thin, not too flexible and easy to solder. It is very important to customize the cables before soldering:
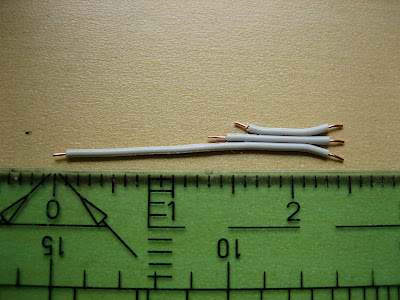
The soldering itself is quite delicate and requires a fairly shake-free hand but is not too difficult. As you can see in the following picture: I am definitely NOT a professional is this discipline ;-))
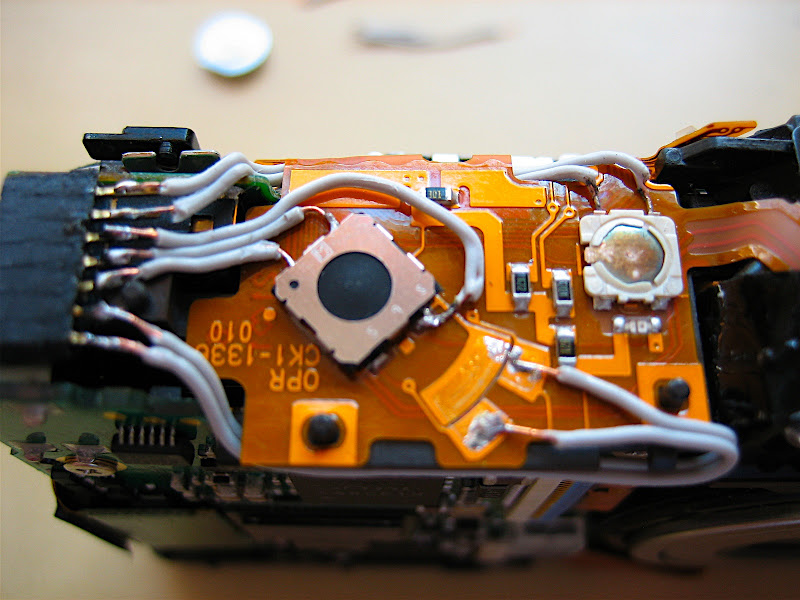
After reassembling the cameras the only visible difference is the missing cover:
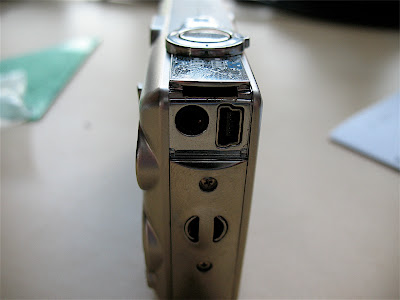
A suitable cable to connect the cameras was soldered using multipin connectors and an old flexible IDE cable. The plugs were made using 2-component epoxy. Not a pretty design but the cable does work ;-)

After a few weeks I found out that the camera behaved strangely when the battery in one of the cameras was running low. I fixed that by cutting one of the connections between the cameras that connected the side of the on-off switch that was directly connected to the batteries. So actually you only need a 6-pin connection between the cameras.